
学生姓名:黄振宇
班 级:车辆2019-06班
指导教师:杜飞龙
毕设题目:基于 UG 的汽车某零件车床夹具设计
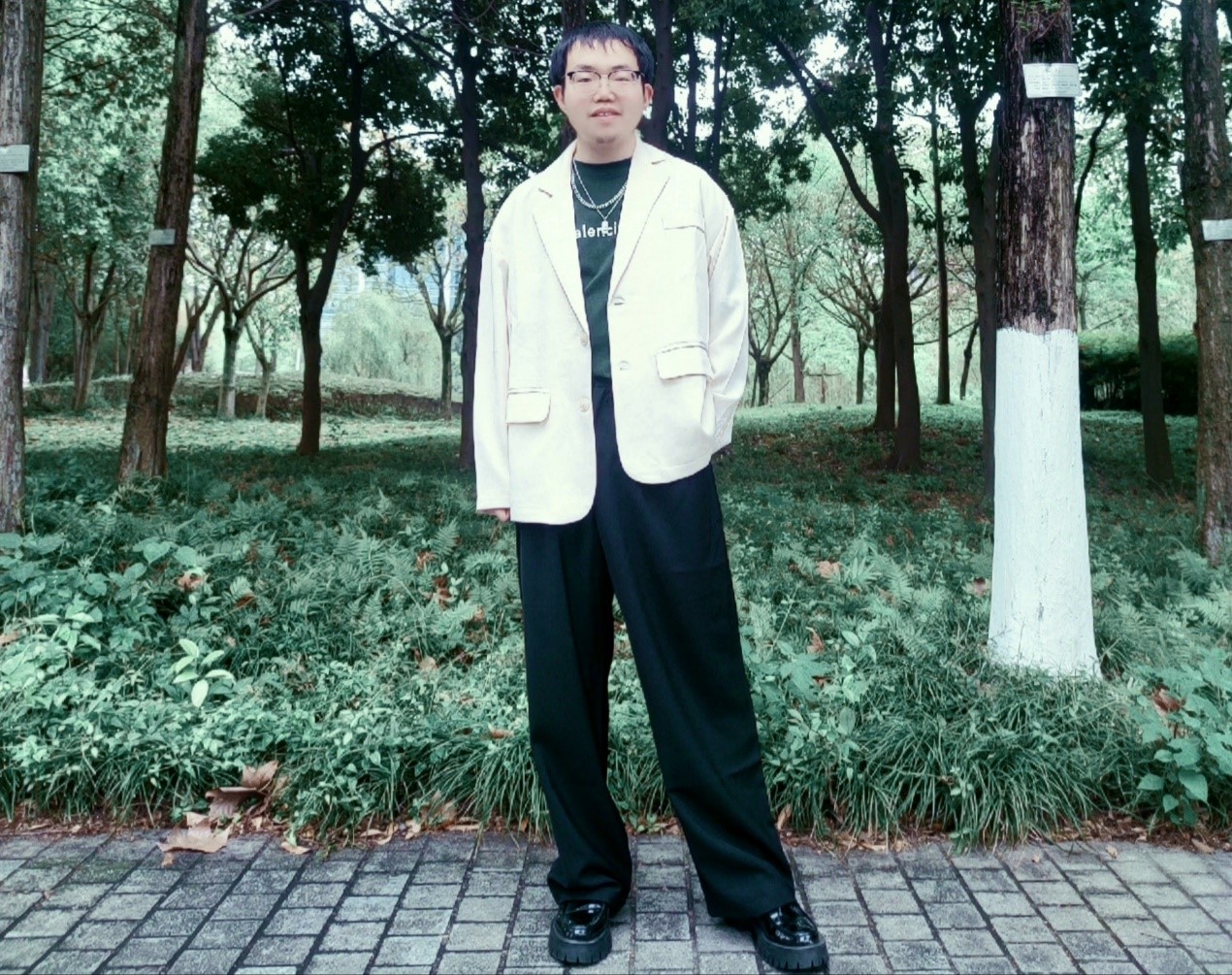

一、选题背景概述
机械制造工业是国民经济的重要组成部分,国家的经济、科技、国防等的发达程度都与此息息相关。随着我国科学技术的飞速发展,与之相配套的机械加工行业发展迅速,产品加工的效率和质量均得到明显的提升。机加工行业的制造生产能力主要取决于制造设备的先进程度,而评价生产设备的指标又包括生产精度、生产效率、运行成本和生产可靠性等。提到生产设备,夹具是无法绕开的一环。优秀的夹具在减少生产成本的同时,大幅提升加工的效率和精度。
国际生产研究协会的统计表明,小批多品种生产的工件品种已占工件种类总数的85%左右。现代生产要求企业所制造的产品品种经常更新换代,以适应市场的需求与竞争。然而,一般企业都仍习惯于大量采用传统的专用夹具,一般在具有中等生产能力的工厂里,约拥有数千甚至近万套专用夹具。现代机床夹具的发展方向主要表现为标准化、精密化、高效化和柔性化等四个方面。对夹具的加工可行性、工件的装夹精度及车削精度、加工便捷性和夹具实用型都提出了更高的要求。
车削加工是在车床上利用工件相对于刀具旋转对工件进行切削加工的方法。车削加工的切削能主要由工件而不是刀具提供。车削是最基本、最常见的切削加工方法,在生产中占有十分重要的地位。在各类金属切削机床中,车床是应用最广泛的一类,约占机床总数的 50%。车床既可用车刀对工件进行车削加工,又可用钻头、铰刀、丝锥和滚花刀进行钻孔、铰孔、攻螺纹和滚花等操作。车削加工在汽车零件制造中也有相当高的使用率。面对当下汽车行业对车削零件精度和专用零件适配度的要求,针对专门零件设计一套专门的、保证精度的、易用的车床夹具就显得尤为重要。
车床夹具是指在车床上用来加工工件内、外回转面及端面的夹具。车床夹具多数安装在主轴上;少数安装在床鞍或床身上。
汽车差速器能够使左、右(或前、后)驱动轮实现以不同转速转动的机构。普通差速器由行星齿轮、行星轮架(差速器壳)、半轴齿轮等零件组成。差速器壳是差速器中起保护作用的外壳,其内弧面的加工以车削加工方法为主流。近年来随着整车制造业的升温,对差速器总成的需求呈攀登态势,差速器壳体的需求不断上升,据统计结果显示 2021年中国差速器市场约 44 亿元。截至 2017 年的情况,国内的差速器制造企业从铸造到加工,工艺水平和产品质量都很难达到生产线统一作业的水平。国内一线车企生产的高质量乘用车仍然多采用外国进口的差速器总成。本选题旨在假定铸造加工符合精度要求的情况下,设计一款尽量能够满足壳体内弧面加工要求的车床夹具。
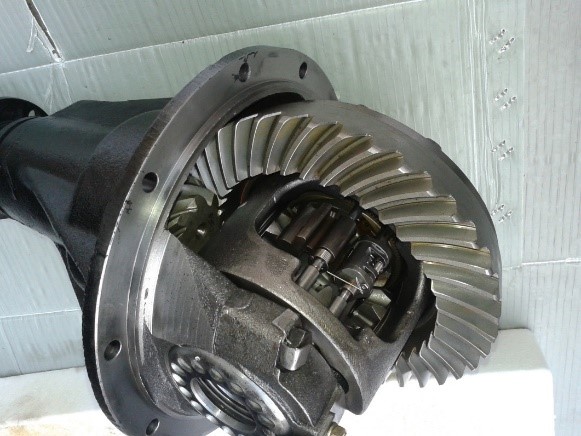
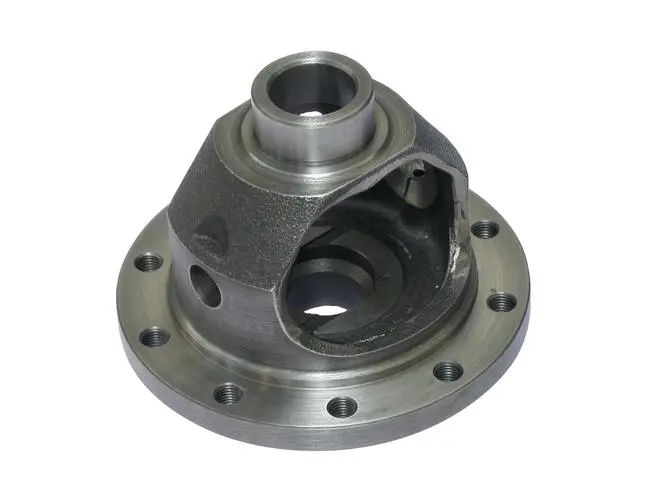
UG(Unigraphics NX)是 Siemens PLM Software 公司出品的一个产品工程解决方案,它为用户的产品设计及加工过程提供了数字化造型和验证手段。这是一个交互式CAD/CAM(计算机辅助设计与计算机辅助制造系统),它功能强大,可以轻松实现各种复杂实体及造型的建构。它在诞生之初主要基于工作站,但随着 PC 硬件的发展和个人用户的迅速增长,在 PC 上的应用取得了迅猛的增长,已经成为模具行业三维设计的一个主流应用。NX 为那些培养创造性和产品技术革新的工业设计和风格提供了强有力的解决方案。利用 NX 建模,工业设计师能够迅速地建立和改进复杂的产品形状, 并且使用先进的渲染和可视化工具来最大限度地满足设计概念的审美要求。NX 包括了世界上最强大、最广泛的产品设计应用模块。 NX 具有高性能的机械设计和制图功能,为制造设计提供了高性能和灵活性,以满足客户设计任何复杂产品的需要。 NX 优于通用的设计工具,具有专业的管路和线路设计系统、钣金模块、专用塑料件设计模块和其他行业设计所需的专业应用程序。目前,相当部分的汽车企业在工业设计和加工工艺分析等领域使用 UG作为辅助软件使用。掌握 UG 软件几乎已经是汽车行业从业人士所需的重要素质。
二、选题总任务及分解
该课程设计的总目标是提交夹具图纸、3D 模型、设计论文(说明书);论文的主要研究工作可以分步为:
1.对差速器壳进行具体选型工作,制作其零件图样及建模。
查阅相关资料,对需要加工的差速器壳进行分析,包括结构、所用材料、技术要求、加工工艺等等。明确差速器的加工步骤和加工工艺;选取其中一个加工步骤(车削壳体内弧面)进行详细了解和设计。在选取一具体型号的差速器壳后,通过参考如《机械精度设计与检测基础》一类资料及根据设计经验明确与该加工工序相关的尺寸、精度、表面粗糙度、设计基准等。作出所选待加工零件的图样,审查零件的公益性,评估该步骤的加工可行性。最后根据图样,于 UG 环境建立三维模型。
2.根据“六点定位法”设计夹紧方案,绘制主要夹紧零件并建模。
根据零件该加工步骤所需的要求综合考量限定自由度的方法,并考虑配合时粗糙度关系、尺寸公差关系等设计出合理的主要起夹紧作用的零件;根据计算所得的切削力设计零件的外形尺寸和材料等。在确定好夹紧零件的尺寸和精度后,绘制出主要零件的零件图样,并建立三维模型,于 UG 环境内与零件模型进行配合,验证无干涉冲突。
3.设计主要夹紧零件与卡盘连接,绘制建模图和总装图。
通过以螺栓为主、各种连接、限位方式为辅的一切合理方法将主要夹紧零件和卡盘相连接,设计出整个夹具的总装方案。在 UG 环境中建立总装配合模型并验证配合无干涉。绘制夹具总装图纸,标注必要的注释和尺寸,对零件名称和材料等规定信息进行详细标注。
4.利用仿真软件对夹具集中受力部件进行有限元分析,验证各个零件的形状、材料、尺寸设计是否能在刚度和强度上达到要求。
首先分析夹具中容易应力集中的零件或部位;将相关三维模型导入 ANSYS 软件环境中,尽量模拟实际情况进行加载;对所选零件和部位进行强度和刚度分析。
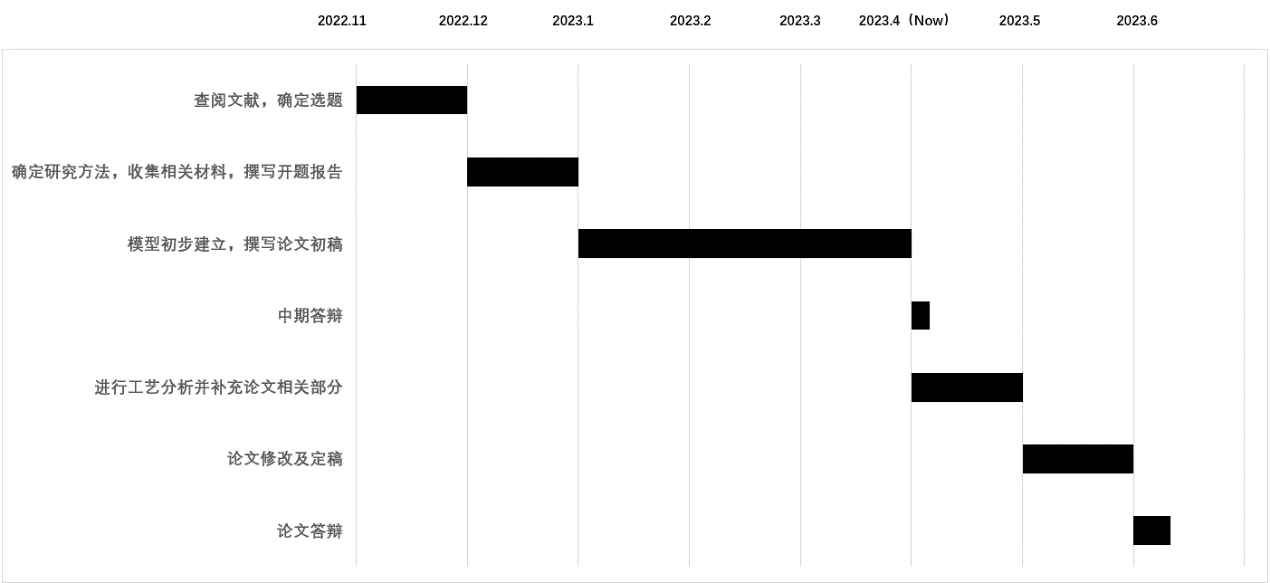
三、已完成的工作
1、完成外文文献翻译:《一种用于机床夹具自动配置的数学方法:分析与综合》(约2 万 5 千字符,翻译文本共计 10646 字)。该文献提供了以螺旋理论为基础的矩阵解法及其判定、验算方法,用数学方法解决夹具的设计及其合理性判别,是非常经典、优秀的工装领域的学术文本。
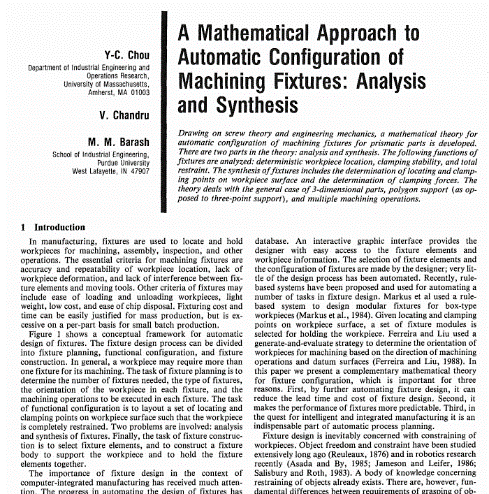
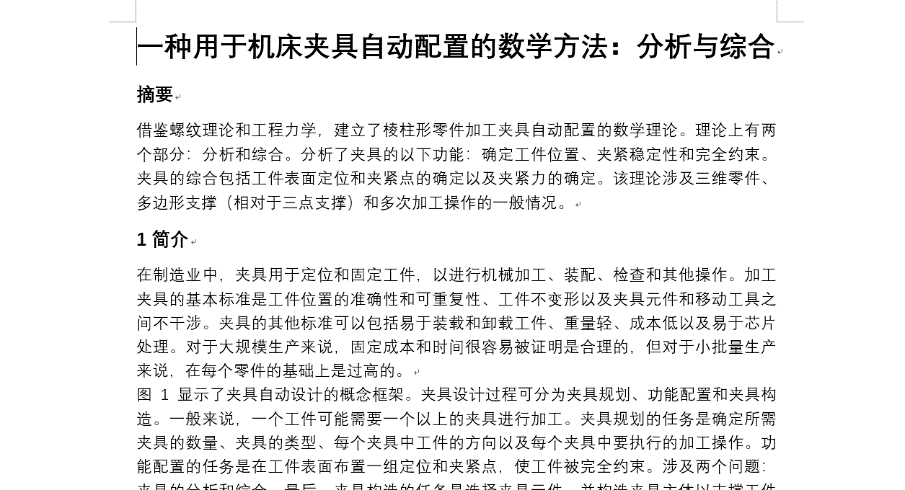
2、了解选题相关国内外现状;了解车削和车床;掌握工件的定位以及夹具的种类、结构、精度;掌握差速器市场现状和质量要求;掌握课设涉及需求的 UG 软件功能的使用分析方法;学习国内外相关设计案例和成品。
3、差速器零件图:
(1) 差速器壳选型(代号 N100-CXQKT)
(2) 精度要求标定——参考《机械精度设计与检测基础》及经验值
(3) 制零件图(比例 2:1;A0)
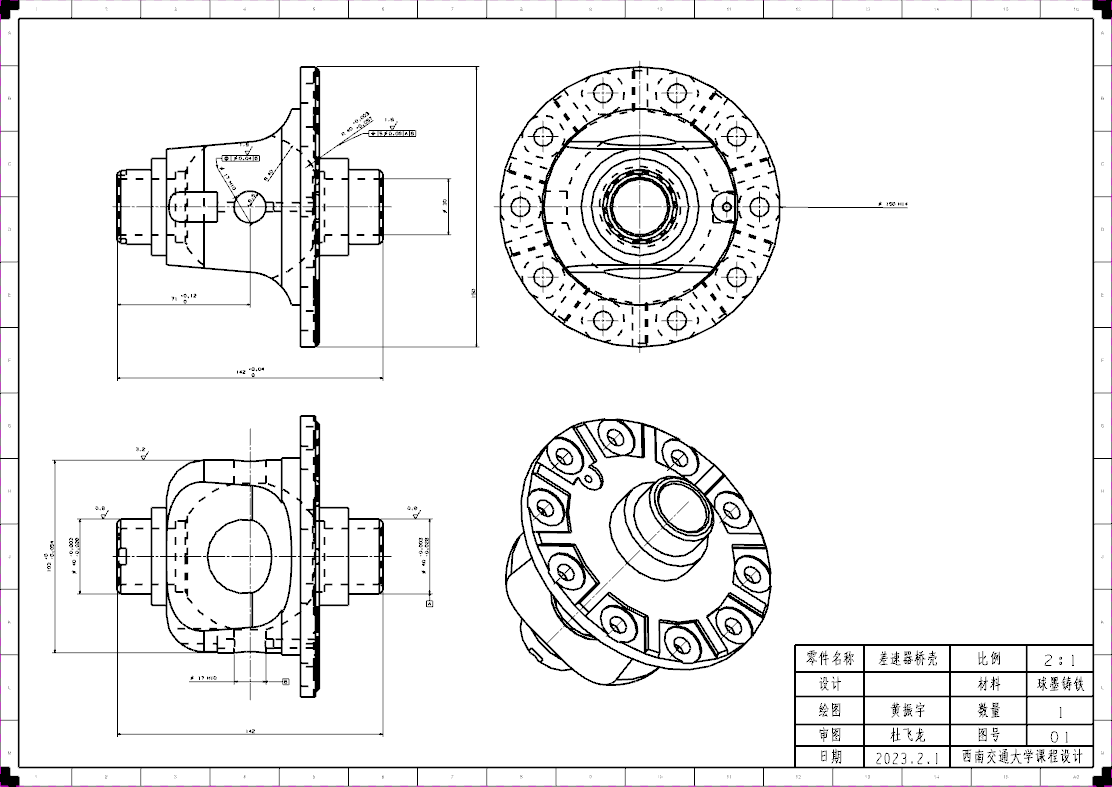
4、差速器在 UG 环境建模;主要夹紧件建模:
(1)夹紧方式确定
(2)夹紧件尺寸设计设计参考切削力的计算和经验取值
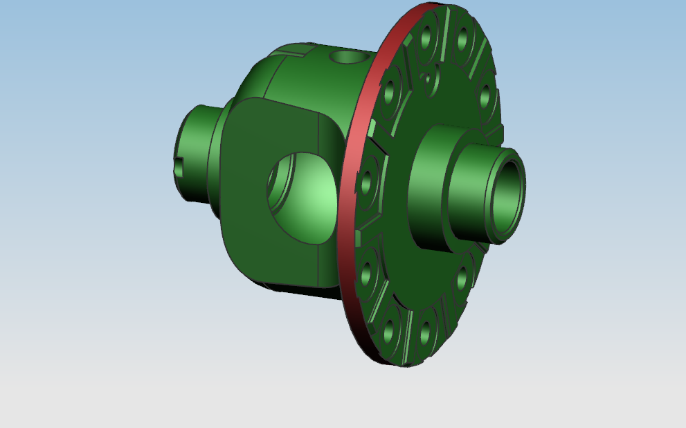
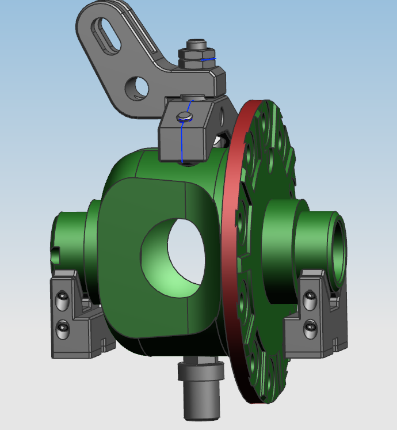
5、夹具总装建模:
(1) 具底座设计建模
(2) 夹具与卡盘装配
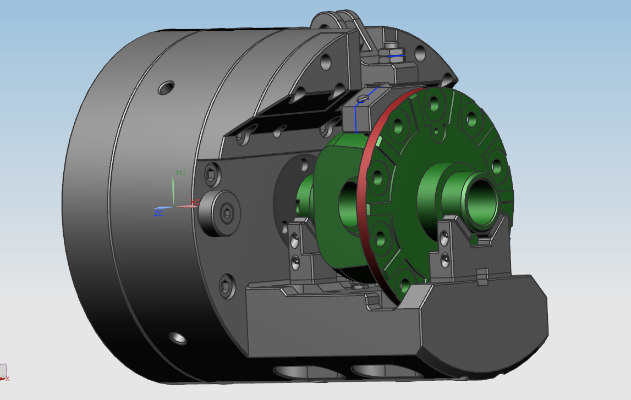
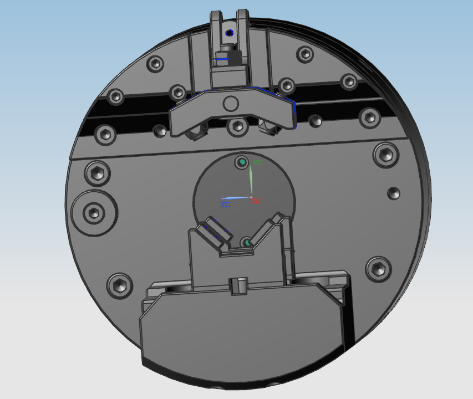
6、主要零件图(完成中);零件总装图(1:1,A0)(完成中):
(1)夹紧件尺寸设计参考切削力的计算和经验取值
(2)若后续仿真结果与预期偏差大,或无法满足加工要求,再次更改零件尺寸。
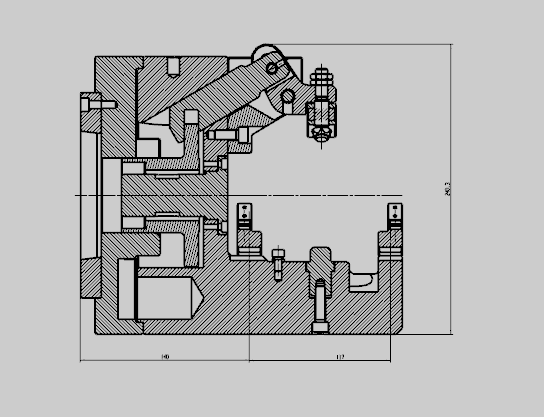
x
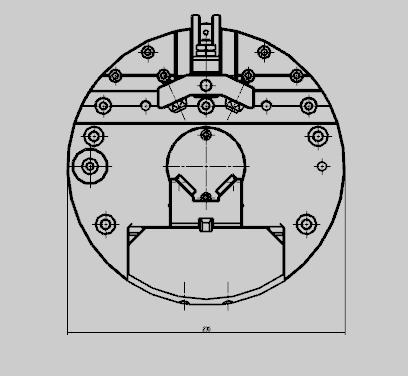
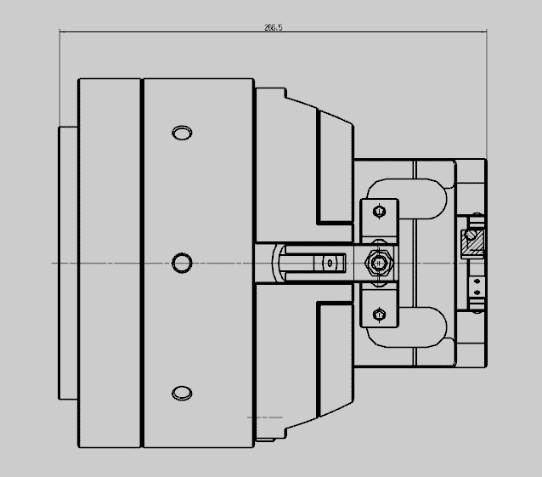
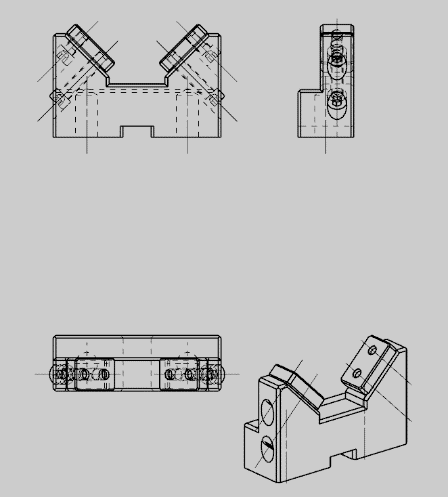
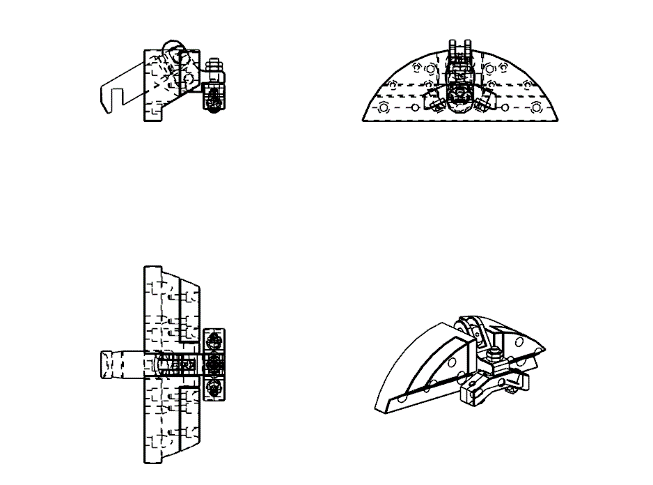
四、下一步工作计划
1、完善零件图纸、进行夹具关键零件的仿真校核。
2、撰写设计说明书
3、修改论文终稿
4、毕业设计答辩

问题一:你现在这个毕业设计选题遇到的最大困难是什么?
回答:是强度、刚度校核。刀面上的切削力计算是相对容易的,但如何将刀面上的切削力转化到夹具关键部位是一个难点,尤其是理论计算。初步考虑是通过几何关系对切削力进行合成分解,再乘以一个系数。由于这一步预计会产生一个较大的误差,所以具体的计算方法还在同老师商量。同时仿真时的加载需要考虑到零件高速旋转带来的尺寸变化和瞬时力冲击等等,如何合理加载也是一个难题。无论是零件关键部位的理论受力计算还是有限元分析,在强度校核方面预计会遇到比较大的推进阻力,最终误差可能也会不尽如人意。希望能够在自己的努力和老师的帮助下,取得一个合理的结果。
问题二:如果最终强度校核的结果判定夹具零件的刚度、强度并不能满足零件工艺要求,你要怎么办?
回答:首先考虑的一定是改变尺寸,最容易出现的问题是零件关键部位(如连接螺栓)的刚度不足,那么此时更换直径更大的螺栓,减小螺栓长度一定是最为便捷的选择。进一步可以选择更换刚度更高的金属材料。在上述两种方法都仍然不可行时,考虑更改零件尺寸、形状设计。但最初设计夹具关键部位尺寸时有参照经验设计和经过初步理论计算,预计大体能够满足需求,不会出现幅度改动。

百里之行,即告段落;千里之行,始于足下。
转眼间四年的大学生涯即将结束,我也迎来了自入学以来就不断设想、不断憧憬的本科生毕业设计(论文)。最终论文选题实际而实用,易懂却并不简单,感谢杜飞龙老师基于以后可能面临的工作需求采用UG作为设计载体。从开题到现在遇到诸多问题,但幸运的是目前为止遇到的问题在同组成员和杜老师的帮助下都得到了暂时性解决。从一年前的机械设计课程设计中我们学到,机械设计的核心大多数情况下不在设计本身。证明设计的可行性,把设计落实到工业生产(甚至是生产线上的易用性、材料外成本等等)往往才是机械设计真正的难点所在。在之前确定差速器壳精度时,我同杜老师经过思考,还是否定了资料上差速器壳与轴承配合处的粗糙度,最终提升了该处的粗糙度等级。一个很小的点或许要花上好些时间,但我觉得这比花同样的时间去建出一个零件模型更加有意义,既然是做产品设计,严谨性是一定需要的态度。
来到大学并不是终点,离开大学更不会是终点,大学生涯是一段教育经历。比专业课知识本身更可贵的,是我在大学学会了如何学习、掌握新兴事物;如何用脚踏实地的态度面对设计;如何在团队中寻求帮助并解决问题。课程设计已经过半,我希望我能够用剩下不多的时间把剩下的工作做完,还要做好。我希望到期终答辩时,我真的能够完成一个完整的、像样的工业产品设计出来,以此给我的大学生涯画上一个完美的句号。